МДК. 02.01 Техническое обслуживание, ремонт и испытание мехатронных систем. Типовые механизмы технологического оборудования.
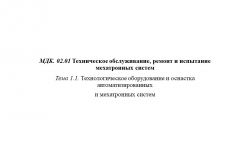
- Рубрика: Презентации / Другие презентации
- Просмотров: 0
Презентация для классов "МДК. 02.01 Техническое обслуживание, ремонт и испытание мехатронных систем. Типовые механизмы технологического оборудования." онлайн бесплатно на сайте электронных школьных презентаций uchebniki.org.ua
МДК. 02.01 Техническое обслуживание, ремонт и испытание мехатронных систем
Тема 1.1. Технологическое оборудование и оснастка автоматизированных
и мехатронных систем
Занятие 3. Типовые механизмы технологического оборудования. Базовые детали и узлы оборудования, виды передач. Классификация, назначение, область применения типовых механизмов технологического оборудования.
Типовые механизмы технологического оборудования.
Технологическая машина - устройство, состоящее из станины или корпуса, привода машины, включающего источник движения - двигатель и
передаточные механизмы, исполнительных механизмов с рабочими органами, которые объединены в единое целое общей станиной или корпусом,
системы управления, регулирования и защиты.
Привод машины включает источник движения - двигатель и передаточные механизмы
Двигатель - это функциональная часть машины, в которой непосредственно происходят физико-химические процессы, связанные с
преобразованием энергии в механическую работу; предназначен для приведения в действие рабочих органов исполнительного
механизма технологической машины.
Передаточный механизм служит для передачи движения от источников движения к рабочим органам исполнительных механизмов.
Основными видами передач являются:
• зубчатые (цилиндрические конические винтовые червячныезубчатоременные)
• ременные (пловтулочно-роликовые зубчатые)
• фрикционные (конические цилиндрические скоременные клиноременные круглоременные зубчатоременные)
• цепные ()
Система управления осуществляет пуск и остановку машины, обеспечивает заданную
последовательности срабатывания рабочих органов в
течении рабочего цикла, выдержку времени, стабилизацию, слежение, выполнение программы,
оптимизацию режимов, синхронизацию работы модулей машины, а также контроль за ее работой
Система регулирования служит для настройки машины на заданный режим или ритм работы
Система защиты используются для предотвращения неправильного включения машины, а также
производственного травматизма
Исполнительный механизм приводит в движение рабочие органы с инструментом
К исполнительным механизмам относятся устройства для:
устройства подачи материалов, заготовок в позицию обработки и удаления из нее полуфабрикатов
или готовой продукции (загрузочное и разгрузочное устройства)
устройства (или средства) перемещения предмета обработки
устройства для приведения в движение основных рабочих органов с инструментом обработки
Рабочий орган непосредственно воздействует на обрабатываемый предмет в соответствии с заданным технологическим процессом.
Рабочими органами являются:
• инструменты
• устройства для установки предмета обработки
• устройства для фиксации предмета обработки
• устройства для перемещения предмета обработки
Отдельные детали машин:
Кривошип - рычаг, который вращается относительно неподвижной опоры.
Коромысло - рычаг, который качается относительно неподвижной опоры.
Шатун - рычаг, который совершает сложное движение и не имеет неподвижной опоры.
Классификация, назначение, область применения типовых механизмов технологического оборудования.
1. Основы кинематической настройки станков
Источник движения и другие механизмы, приводящие в движение исполнительный орган станка,
называется приводом движения. Приводы могут реализовывать главное движение, подачу,
вспомогательные и согласующие движения с заданной характеристикой изменений скорости.
Изменение скорости может быть ступенчатым или бесступенчатым.
С учетом необходимости получения оптимальных по режимам резания скоростей для различных
диаметров обработки привод должен обеспечивать любую частоту вращения шпинделя:
(1)
(2) в пределах выбранного диапазона регулирования.
В пределах диапазона регулирования станок должен обеспечить любую частоту вращения, т е требуется бесступенчатое регулирование частоты вращения
Существующие способы бесступенчатого регулирования отличаются повышенной стоимостью, а при использовании механических вариаторов — низкой надежностью и повышенными потерями
Поэтому в настоящее время в станках чаще всего применяют приводы со ступенчатым регулированием с асинхронными нерегулируемыми электродвигателями
Основные их достоинства — небольшая стоимость, высокий КПД, компактность, возможность получения постоянной мощности на всем диапазоне регулирования.
При этом промежуточные значения частот вращения в пределах диапазона регулирования выбирают по закону геометрической прогрессии.
Малые значения знаменателя приводят к существенному усложнению привода, и вместо них выгоднее применять бесступенчатое регулирование, поэтому φ = 1,06 в станках практически не применяют; φ = 1,12 применяют в станках с ЧПУ и тяжелых, где требуется точная настройка на заданный режим. Наибольшее распространение получили значения φ = 1,26 и φ = 1,41, которые принимаются при разработке приводов универсального оборудования; φ = 1,58 и φ = 1,78 применяют в специализированных станках, где велико вспомогательное время и поэтому точная установка скорости не обязательна; φ = 2 практически не применяют.
Переход от меньшего знаменателя к большему ведет к увеличению потерь из-за снижения производительности при резании Поясним на примере. Предположим, что при расчете по формуле (1) получена частота вращения шпинделя 370 мин-1, а ближайшие значения у привода 315 и 400 мин-1. Если придерживаться обычной практики округления, то надо установить n = 400 мин-1, но в таком случае режущий инструмент будет работать с перегрузкой и выйдет из строя раньше рассчитанного срока. Замена инструмента и его переточка потребуют времени больше, чем удастся сэкономить за счет повышения оборотов (здесь экономия составит всего 400/370 = 1,08 → 8 % от времени резания). Поэтому принимают значение 315 мин-1 и теряют 17 % от времени резания, но в целом выигрывают за счет уменьшения времени на переустановку инструмента и увеличения его стойкости Увеличение знаменателя φ от 1,06 до 2 ведет к росту потерь за счет снижения производительности резания с 5 до 50 %
2. Приводы ступенчатого регулирования главного движения
Привод ступенчатого регулирования с шестеренной коробкой скоростей является наиболее распространенным типом. Он легко встраивается в шпиндельную бабку, что делает конструкцию компактной. Ступенчатый привод обеспечивает концентрацию органов управления и упрощает изготовление коробки Но есть у него и недостатки:
вибрации, возникающие из-за дефектов в зубчатых передачах и распространяющиеся на шпиндель, что повышает шероховатость обработки;
нагрев шпиндельной бабки из-за трения в зубчатых передачах.
Он продолжается от 3 до 5 часов, пока не наступит стабилизация, и за это время происходит постепенное смещение оси шпинделя. К счастью, оно невелико: наибольшее его значение (для токарного станка) 10. . .11 мкм, что составляет небольшую долю допуска на изготовление большинства деталей.
Кроме названных способов, ступенчатое изменение скорости движения может осуществляться ступенчатыми шкивами (настольные сверлильные станки), многоскоростными асинхронными электродвигателями (обычно они имеют две скорости, но может быть до четырех: 3000 — 1500 — 1000 — 750 мин-1) или комбинацией механизмов.
Шестеренные коробки скоростей применяются и как самостоятельные узлы в станках с разделенным приводом, и как составная часть шпиндельной бабки или механизма подачи (встроенные коробки) . Для изменения скорости движения резания и подачи почти всегда используют не один тип механизмов передачи движения, а определенную комбинацию из типовых устройств, являющуюся для данного привода станка наиболее оптимальной.
Приводы ступенчатого регулирования движения подачи
Вторым по значению приводом в станках является привод подач В зависимости от назначения станков и методов формообразования поверхностей механизмы подач осуществляют прямолинейное или вращательное движение. Эти приводы в большинстве случаев являются тихоходными, а при резьбонарезании, обкатке и делении — высокоточными. Требования, предъявляемые к механизму подач (число ступеней, их диапазон, характер движения, частота переключений, накопленная погрешность), влияют на структуру и конструкцию коробок подач. Как и приводы главного движения, коробки подач могут быть со ступенчатым и бесступенчатым регулированием К ступенчатым коробкам подач относятся те же механизмы, что и к коробкам скоростей:
коробки подач с передвижными колесами и блоками;
коробки скоростей с кулачковыми муфтами;
коробки скоростей с фрикционными муфтами;
коробки подач со сменными колесами.
Кроме этих механизмов, применяют также:
коробки подач со встроенными ступенчатыми конусами колес и вытяжной шпонкой;
коробки подач с нортоновскими конусами;
коробки подач с механизмом типа «меандр»;
коробки подач с гитарами сменных колес.
Для осуществления прямолинейного движения после коробки подач устанавливают следующие механизмы:
ходовой винт — гайка, зубчатое колесо — рейка, червяк — рейка, кулачок, шатунный и рычажный механизмы;
гидравлические и пневматические двигатели типа поршень — цилиндр или пневмокамеры;
электромагнитные устройства в виде линейно развернутых электродвигателей, бесконтактных электромагнитных передач, соленоидов
4. Приводы бесступенчатого регулирования движения
Основные достоинства приводов с бесступенчатым регулированием — повышение производительности обработки за счет точной настройки на режимы резания, возможность плавного изменения скорости во время работы, простота автоматизации переключения скоростей Для бесступенчатого регулирования скорости иногда применяют фрикционные вариаторы, чаще — регулируемые двигатели. Наличие проскальзывания в вариаторе приводит к изменению передаточного отношения и к износу Для большинства вариаторов диапазон бесступенчатого регулирования R6 = 4. . . 6. Фрикционные передачи в большинстве случаев предназначены для мощностей, не превышающих 200 кВт, окружная скорость катков допускается до 25 м/с. На малой скорости резко падает КПД. Надежность вариаторов уменьшается и с увеличением передаваемой мощности КПД вариаторов от 0,65 до 0,95, удельный объем 5. . . 20 дм3/кВт, коэффициент неравномерности хода 0,001-0,1. Передачи с механизмом самозатягивания могут обеспечить почти жесткую характеристику регулирования скорости.
В станкостроении применяют различные виды этих машин, например вариатор с раздвижными конусами Выполняется с различным видом связи С (рис. 5) . Это могут быть стандартные или специальные клиновые ремни, специальная цепь или стальное кольцо трапециевидного сечения. Плавное изменение скорости выходного шкива Ш3 в диапазоне 4. . . 8 достигается одновременным раздвиганием одной и сближением другой пары конусов. При этом изменяются диаметры рабочей части ведущих (Ш^ и ведомых (Ш2) конусов.
В приводах вспомогательных движений применяются одинарные или сдвоенные (рис. 6) торцовые (лобовые) вариаторы. Движение от вала 6 через диски 5, подвижные ролики 3 и диск 2 передается выходному валу. Бесступенчатое изменение скорости вращения выходного вала достигается за счет перемещения роликов 3 вдоль винта 4 вращением за выходной четырехгранный конец 7 винта 4. Стрелка 8 указывает значение передаточного отношения. Лобовые вариаторы применяют в станках, винтовых прессах и приборах. Они имеют интенсивный износ рабочих поверхностей катков и пониженный КПД вследствие разности скоростей на площадке контакта. Некоторые конструкции лобовых вариаторов позволяют не только плавно изменять угловую скорость ведомого вала, но и менять направление его вращения.
Кроме описанных вариаторов, применяют тороидный вариатор, вариатор с наружным и внутренним коническими шкивами, торцеконический вариатор (рис. 7). Шкивы сжимаются рабочими поверхностями с усилием F. При изменении передаточного отношения радиус ведущего шкива R! остается постоянным, изменяется радиус ведомого шкива R2 .
Кроме механических бесступенчатых регуляторов скорости (вариаторов), применяют системы генератор — двигатель и электромашинные усилители. В последнее время широко используют цифровое тиристорное регулирование асинхронных трехфазных электродвигателей с фазным ротором путем изменения напряжения питания. Так делают на станках с ЧПУ, многооперационных станках.
В шлифовальных станках для бесступенчатого изменения скорости перемещения стола используется гидравлический привод в виде гидроцилиндра (рис. 8), двигателя с возвратно-поступательным движением ведомого звена (штока, плунжера или корпуса) Питается гидроцилиндр от гидростанции, включающей асинхронный электродвигатель переменного тока, соединенный с гидравлическим насосом, который с помощью пускорегулирующей аппаратуры подает масло в полости гидравлического цилиндра, соединенного с рабочими органами станка. Регулирование может быть дроссельным, объемным, объемно-дроссельным или за счет изменения скорости двигателя, приводящего в работу насос; ручным или автоматическим. В зависимости от задач регулирования гидропривод может быть стабилизированным, программным или следящим.
Бесступенчатое изменение скорости осуществляется за счет изменения количества масла как подаваемого насосом, так и потребляемого гидравлическим цилиндром. Гидропривод вращательного движения с гидромотором задает вращательное движение ведомому звену (валу или корпусу).
Бесступенчатые коробки подач дают возможность:
настраивать с большой точностью режим обработки без остановки станка;
сохранить постоянную скорость при поперечном точении и шлифовании;
синхронизировать обработку на нескольких станках автоматической линии
5. Реверсирование движения механизмов
Большинство рабочих органов станков в процессе их работы должны изменять направление своего движения. Для этой цели служат различные виды реверсивных механизмов (трензели). Если допускается реверсирование всей цепи привода, то изменение направления движения рабочего органа очень просто может быть осуществлено реверсированием вращения ротора электродвигателя. При использовании асинхронного электродвигателя трехфазного тока в этом случае достаточно с помощью переключателя поменять местами две фазы, как это делается, например, на вертикально-сверлильных станках, а для реверсирования электродвигателя постоянного тока надо изменить полярность тока.
Реверс с одним паразитным колесом показан на рис. 2. Этот механизм выполняется в различных вариантах, однако принцип его работы остается неизменным. В токарно-винторезном станке 16К20 прямое вращение от ведущего вала I через муфту М1, включенную влево, передается зубчатыми колесами с z = 54 — z = 39 вала II к ведомому валу III. Во время работы токарь рукояткой включения вращения шпинделя может сместить муфту М1 вправо. При этом передача z = 54 — z = 39 не получает движения от вала I и вращается вхолостую, а движение будет передаваться по цепи: вал I — муфта М1 — колеса z = 50 — z = 24 — z = 36 — z = 38 — вал III. Направление движения шпинделя изменится на противоположное.
Реверс с двумя паразитными колесами (рис. 9) представляет собой механизм, состоящий из четырех цилиндрических колес, смонтированных в подвижной рамке 1, которая может находиться в трех положениях. В первом положении (позиция а) вращение от ведущего колеса z1 к ведомому колесу z4 передается через паразитные колеса z2 и z3, и поэтому колесо z4 вращается в направлении, противоположном направлению вращения колеса z4. Во втором положении (позиция б) ведущее колесо z1 не зацепляется ни с одним из паразитных колес, и поэтому ведомое колесо z4 не вращается В третьем положении (позиция в) паразитное колесо z3 непосредственно входит в зацепление с ведущим колесом z1, а колесо z2 вращается вхолостую, не принимая участия в передаче движения В этом случае ведущее и ведомое колеса вращаются в одну и ту же сторону.
В зуборезных станках для нарезания конических зубчатых колес с круговыми зубьями реверсирование обкатной люльки обеспечивается механизмом, имеющим составное зубчатое колесо z5 (рис. 10) . При вращении шестерни z2 в одном направлении движение посредством вала II и конической передачи z3 — z4 передается приводному колесу z5, которое также имеет постоянное направление вращения. При зацеплении колеса z5 с сектором внутреннего зацепления составного колеса z6 последнее получает вращение в одном направлении; далее при проходе колеса z5 через зацепление с одним из соединяющих участков составного колеса происходит процесс реверсирования; при зацеплении колеса z5 с сектором внешнего зацепления составного колеса последнее вращается в противоположную сторону. Для обеспечения возможности зацепления колеса z5 со всеми участками составного зубчатого колеса z6 вал III с колесами z3 — z4 и колесом z5 могут перемещаться с кареткой К в радиальном направлении.
реверс с одним паразитным колесом и двусторонней кулачковой муфтой (рис. 11, а). Он характерен тем, что все его цилиндрические зубчатые колеса могут быть выполнены как с прямыми, косыми, так и с шевронными зубьями;
реверс с одним паразитным колесом и двойным подвижным блоком шестерен (рис. 11, б). Может быть выполнен только с цилиндрическими колесами, имеющими прямые зубья;
реверс с одним широким паразитным колесом (рис. 11, в). Отличается от предыдущих механизмов тем, что имеет четыре колеса вместо пяти и колеса z1, z2 и z4 имеют равные числа зубьев, чем обусловливается одинаковая скорость вращения ведомого вала III как в одну, так и в другую сторону;
конический реверс с подвижным блоком конических колес (рис. 11, г). Вал I имеет постоянное направление вращения. Когда блок конических колес, связанный с валом I направляющей шпонкой, находится (как показано на схеме) в левом крайнем положении, в зацеплении участвуют колеса z2 — z3 и вал II вращается по стрелке б. При перемещении блока конических колес вправо зацепляются колеса z1 — z3 и вал II начинает вращаться по стрелке а;
конический реверс с двусторонней кулачковой муфтой Мк (рис. 11, д). Работает по аналогичному принципу, только в этом механизме изменение направления вращения вала II достигается переключением муфты Мк;
реверс с колесом внутреннего зацепления (рис. 11, е). Вал I с колесом z1 постоянно вращается в одном направлении, приводя в движение колеса z2 и z3, которые при этом вращаются в разных направлениях. Перемещением двусторонней кулачковой муфты Мк вправо или влево можно сообщить валу II вращение в ту или иную сторону
6. Механизмы суммирования движений
Для суммирования движений на одном звене в кинематические цепи некоторых станков вводят спецмеханизмы: винтовые пары, реечные и червячные передачи, дифференциалы с цилиндрическими и коническими зубчатыми колесами. Эти механизмы позволяют увеличить диапазон настройки цепей с целью расширения технологических возможностей затыловочных, зуборезных, резьбошлифовальных и других станков. Один из дифференциальных механизмов показан на рис. 12. На валах I и III жестко установлены зубчатые колеса z1 и z4. Полый вал II имеет водило 1, в которое вмонтирован сателлитный вал с колесами z2 и z3 . Движение любых двух валов может суммироваться на третьем валу. Наиболее часто в практике станкостроения суммируют вращение валов I и II.
Суммарное вращение ведомого вала III можно представить состоящим из двух движений: первое он получает от вала I при неподвижном вале II, второе — от вращения вала II при неподвижном вале I. Вал I передает вращение по цепи колес z1/z2 · z3/z4 . При вращении вала II с водилом сателлитное колесо z2, обкатываясь вокруг неподвижного колеса zy, получает вращение вокруг своей оси, которое передает валу III при помощи передачи z3/z4 . Передаточное отношение от ведущих звеньев I и II к ведомому III
iI-III = z1z3/z2z4; iII-III = 1 — z1z3/z2z4.
Для решения аналогичных задач распространен и конический дифференциал (рис. 13) привода быстрых перемещений стола и бабки бесконсольного фрезерного станка модели 6А54, где рабочие перемещения осуществляются от вала I через червячную передачу а2 — z2 и коническую передачу z3 — zc — z4 . Быстрые перемещения производятся электродвигателем М, через червячную передачу a1 — z1, Т-образный вал II и планетарную коническую передачу zc — zc — z4
В качестве суммирующих механизмов применяются червячные механизмы В червячном дифференциальном механизме, показанном на рис. 14, червяк z1, жестко связанный с валом I, вращается в зацеплении с червячным колесом z2, вращающимся вокруг вала II.
Вал I имеет возможность поступательного перемещения в подшипниках. Рычаг 1, вращающийся вокруг неподвижной оси, пальцем 2 скользит в кулисе 3 вала I. Угловое перемещение колеса z2 может быть получено как сумма двух вращательных движений: движения, получаемого от червяка г\ при его вращении, и движения, получаемого от червяка z1 при его поступательном движении вдоль оси вала I. При поступательном движении червяк z1 работает как зубчатая рейка.
7. Механизмы прерывистых движений
Довольно часто при непрерывном движении большинства узлов станка отдельным его агрегатом надо сообщать прерывистое движение, например, для поворота шпиндельного стола (как в вертикальных многошпиндельных токарных полуавтоматах), шпиндельного блока (как в горизонтальных многошпиндельных токарных автоматах), револьверной головки. В кинопроекторах это необходимо для остановки кадра перед объективом и т. д. В станкостроении прерывистые движения получают, используя различные типовые механизмы, каждый из которых имеет свою область применения. Эти механизмы могут давать малые и большие перемещения. Наибольшее распространение среди этих механизмов получили храповые и мальтийские.
Храповые механизмы позволяют весьма тонко и в широком диапазоне изменять величину периодических перемещений рабочих органов станков. Механизм с наружным храповым колесом (рис. 15) находит применение в поперечно-строгальных станках. При равномерном вращении кривошипа 1 связанный с ним шатуном 2 рычаг 3 получает непрерывное качательное движение относительно оси. С рычагом 3 связана собачка 5, упирающаяся в зубья колеса 4. При качании рычага влево собачка, упираясь в один из зубьев колеса, поворачивает его на некоторый угол При качании рычага вправо собачка приподнимается, скользит по спинкам зубьев и колесо не поворачивается. С помощью шибера 6 можно ограничить число зубьев храпового колеса, с которыми может взаимодействовать собачка, и тем самым регулировать угол поворота храпового колеса.
Механизм с торцовой храповой муфтой (рис. 16) применяется в приводе подач продольно-строгальных станков 7231А. При непрерывном и равномерном вращении вала I с кривошипом 1 зубчатое колесо 3 и вал II получают через шатун и рейку 2 вращение в обе стороны. На валу II на направляющей шпонке установлена храповая муфта 5, которая пружиной 4 поджимается к зубчатому колесу 6, имеющему храповые зубья на торце ступицы. При перемещении рейки 2 вверх и соответствующем вращении вала II храповая муфта, преодолевая сопротивление пружины, отходит влево и не передает вращение колесу 6, а при перемещении рейки вниз вал II вращается так, что храповая муфта сцепляется со ступицей колеса 6 и вращает его по стрелке.
Храповой механизм, аналогичный показанному на рис. 15, но с поршневым приводом, применен в приводе радиальных подач круглошлифовального станка модели 3151. В этом механизме собачка 5, находящаяся в зацеплении с храповым колесом 4, установлена в пазу штока пневмоцилиндра Под действием сжатого воздуха поршень со штоком и собачкой перемещается возвратнопоступательно При перемещении штока вправо храповое колесо 4 поворачивается на один или несколько зубьев по стрелке При обратном ходе штока с собачкой храповое колесо не вращается.
Аналогичный храповой механизм, но только с приводом от соленоида, применен на внутришлифовальном станке модели 2А252 Иногда технологическая операция предполагает остановку механизма в одном положении, а затем перемещение с большой скоростью в следующее положение. Наиболее часто это требуется в поворотно-делительных столах. Эту работу с успехом выполняет мальтийский механизм (рис. 17), состоящий из крестообразной основы 1 с равномерно расположенными радиальными пазами и кривошипа 4 с цевкой 3. При вращении кривошипа цевка входит в паз креста, поворачивая его на угол, обусловленный заданной схемой После выхода цевки из паза крест останавливается и стопорится сектором 5, который находится в выемке 2 креста до тех пор, пока цевка не войдет в следующий паз. Тогда движение возобновляется Наименьшее число пазов равно 3 На практике применяют кресты с 4, 6, 8 пазами. Поворот можно выполнять не только на равные, но и на разные углы. Кривошип может иметь не одну, а несколько цевок.
Кроме мальтийских механизмов с наружным зацеплением, нашли применение механизмы с внутренним зацеплением. Их конструкция более компактна При необходимости передать движение под углом применяют другие разновидности мальтийских механизмов (рис. 18). Вал 1 вращается вокруг неподвижной оси А, цевка а периодически входит в прорези b на сферической поверхности мальтийского креста 2, вращающегося вокруг оси В. Запирающая дуга d входит в вырезы с креста и скользит по ним в периоды его покоя.
Преобразование постоянного вращательного движения одного вала в прерывистое движение второго вала легко реализуется с помощью зубчатого колеса и зубчатого сектора (рис. 19). Колесо 1, закрепленное на валу 2, периодически поворачивается только в течение того времени, когда его зубья находятся в зацеплении с зубьями зубчатого сектора 3, установленного на валу 4. В этом механизме не представляется возможным регулировать угол поворота колеса, но можно получить несколько поворотов за счет наличия не одного, а нескольких зубчатых секторов 5 и 6. Зубчатых секторов может набраться на целое колесо, и их положение можно регулировать, поворачивая относительно оси 4
Прерывистые движения обеспечивают механизм с однооборотной муфтой, шаговый электродвигатель и множество механизмов, похожих на мальтийский и зубчатый
8. Механизмы деления
Для деления заготовки на равные части или заданные углы и для поворота механизмов станков применяют делительные механизмы В последнем случае часто используются уже названные мальтийские и храповые механизмы, а также рычажные механизмы. Деление заготовки выполняют с помощью:
упрощенных делительных приспособлений для непосредственного деления (рис. 20);
универсальных делительных головок (рис. 21);
оптических делительных головок;
многошпиндельных (двух-, трех-, четырехшпиндельных) делительных головок, которые применяют в серийном производстве
Кроме того, существует множество других механизмов для деления.
На рис. 20 представлены элементарные механизмы деления. В первом (рис. 20, а) угловое фиксирование шпинделя 3 производится фиксатором 1 в пазах-отверстиях диска 2. Это механизм непосредственного деления. На рис. 20, б отсчет углового поворота шпинделя 5 определяется по градуированной шкале лимба 1 и неподвижному нониусу 2. Поворот шпинделя осуществляется маховиком 4, а рукояткой 3 фиксируется в нужном положении.
Широкое применение получили механизмы деления, состоящие из червячной пары, где отсчет углового поворота определяется по градуированной круговой шкале При вращении червяка 5 (рис. 20, в) происходит угловой поворот червячного колеса 3 и жестко связанного с ним шпинделя с поворотным столом 1 со шкалой 2, по которой производится точный отсчет углового поворота с помощью нониуса 4.
На рис. 20, г показан простейший случай применения пневматического (гидравлического) привода. Конец поршня пневмоцилиндра 1 выполнен в виде рейки 2, которая находится в зацеплении с зубчатым сектором 3, свободно сидящим на валу. Собачка 5 жестко соединена с зубчатым сектором 3, а храповое колесо 6 и делительный диск 4 закреплены на валу При поступательном перемещении рейки зубчатый сектор с помощью собачки 5 поворачивает храповое колесо и, соответственно, вал с делительным диском Требуемый угол поворота ограничивается фиксатором 8 по пазам делительного диска При обратном ходе поршня рейка возвращает собачку в исходное положение. Отвод фиксатора из паза делительного диска производится автоматически одновременно с подачей воздуха в цилиндр.
Деление, особенно точное, требует специальных механизмов. В конструкциях продольных и круговых делительных машин широко используются храповые механизмы, работающие в сочетании с точными винтовыми или червячными передачами. На рис. 22 приведена кинематическая схема электромеханического привода автоматической продольной делительной машины МДА-1, предназначенной для нанесения делений на металлические и стеклянные заготовки шкал длиной до 250 мм с расстоянием между штрихами от 0,1 до 1 мм. Предельная погрешность интервалов между двумя соседними штрихами не превышает 3 мкм.
В станине 1 на подшипниках скольжения вращается ходовой винт 2. Осевые усилия на винт воспринимаются подпятником, а зазор в микрометрической паре выбирается с помощью грузов, подвешенных к рабочему органу Перемещение стола обеспечивается микрометрической парой. Гайка 4 перемещается вдоль винта вместе со столом Ошибки изготовления ходового винта 2 компенсируются при помощи устройства 3, состоящего из коррекционной линейки и рычага с контактным роликом.
С ходовым винтом связано храповое колесо 18, поворот которому сообщается собачкой 19 от кривошипного механизма. Делительное колесо поворачивается на угол, необходимый для перемещения заготовки на шаг. Для удержания ходового винта от случайных поворотов служит защелка 14, которая отсоединяется кулачковым устройством 13 перед перемещением заготовки.
При повороте рычага поворачивается гайка 4 и гайка со столом перемещается на величину ошибки. Стол 5 при вращении ходового винта перемещается по направляющим станины. Заготовка 6 устанавливается на опоре, закрепленной на столе.
Поперечный суппорт 8 с резцедержателем и механизмом подъема и опускания резца 7 закреплен на вертикальном кронштейне. Возвратно-поступательное движение резцу придает кривошип, приводимый в движение от горизонтального валика 9, который получает вращение от мотора Для подъема резца при перемещении заготовки и для опускания его при нанесении риски на заготовку служат тяга 12 и кулачок 11.
Длина штриха задается кривошипно-шатунным механизмом 10. В левой части распределительного валика расположен кривошип 15, связанный тросом 16 через барабан с качающимся рычагом 17, на конце которого укреплена собачка 19
9. Предохранительные устройства
В ходе работы станка по разным причинам могут возникнуть перегрузки, грозящие поломкой.
Чтобы избежать этого, станки оснащают предохранительными устройствами, которые по назначению можно разделить на три группы:
предохранительные устройства от перегрузки;
блокировочные устройства от неверного включения;
ограничители хода узлов.
Защита механизмов от перегрузки сводится к ограничению действующих нагрузок электрическими, гидравлическими и механическими предохранительными устройствами. Электрические устройства реагируют на возрастание тока — это плавкие предохранители и тепловые реле. Гидравлические срабатывают от возросшего давления — это предохранительные клапаны.
Механические предохранительные устройства при редких перегрузках обычно разрушаются (таковы шпонки и штифты — рис. 23), а при частых — срабатывают (кулачковые, шариковые, фрикционные и другие муфты) . Шариковые муфты проще и надежнее кулачковых, но фрикционные — мощнее. Рассмотрим устройство и работу некоторых из них.
В токарно-револьверном станке модели 1К341 в качестве устройства для предохранения от перегрузок револьверного суппорта применяется механизм падающего червяка (рис 2 44)
Рабочая подача выключается тогда, когда суппорт доходит до неподвижного упора, установленного на станке в соответствии с техпроцессом, и дальше не может перемещаться. При этом приводной вал 10 продолжает передавать вращение червяку 7. При недопустимом возрастании нагрузки полумуфта 5 благодаря скошенным зубьям отходит влево, преодолевая сопротивление пружины 15, и нажимает через упор 14 на рычаг 4, который при помощи выступа 13 вместе с рамкой 12 через шарнир 8 и вал 16 поддерживает червяк 7 в зацеплении с червячным колесом 11 В момент, когда полумуфта 5 отодвинется влево от полумуфты 6 настолько, что выступ 13 не будет поддерживать рамку 12 и червяк 7 с валом 16, устройство под действием собственного веса упадет вниз по стрелке 2 до упора 3, поворачиваясь относительно оси шарнира 9, и червяк выйдет из зацепления с червячным колесом. После того как токарь отведет револьверный суппорт вправо от упора, он может, потянув за рукоятку 1 по стрелке 17, опять включить подачу суппорта.
Существует несколько конструкций падающих червяков.
Самовыключающиеся кулачковые муфты (рис. 25) служат тем же целям, что и падающие червяки. Зубчатое колесо 1, являющееся ведущим, связано через шпонку 2 с полумуфтой 3. Вторая полу- муфта 5 с помощью пружины 6 прижата к полумуфте 3 скошенными кулачками 4. Силу сжатия пружины регулируют смещением стакана 7 по резьбе 8. В случае возникновения больших тангенциальных сил кулачки 4 полумуфт начинают смещаться относительно друг друга и осевая составляющая силы сжимает пружину Полумуфта 5 при дальнейшем вращении колеса 1 будет отжиматься вправо и выйдет из зацепления с полумуфтой 3. Ведомый вал 9 перестанет вращаться. Предохранительное устройство может отключать или ограничивать нагрузку Отключающее предохранительное устройство (рис. 26) выполняют в виде разрушающегося элемента — болта, соединяющего две детали. На рисунке шатун зажимного механизма горизонтально-ковочной машины состоит из звеньев 2 и 3, соединенных шарнирно и болтом 1 При предельном сжатии шатуна болт разрывается и звенья 2 и 3 совершают относительное движение и «складываются». Механизм приобретает лишнюю степень свободы, и звенья не нагружаются.
10. Блокирующие устройства и ограничители хода
Блокирующие устройства, устанавливаемые на станках, предотвращают ошибочное включение в работу механизмов, если это представляет угрозу работе оборудования. Таким может быть, например, включение подачи стола при неподвижном шпинделе фрезерного станка или одновременное включение движения суппорта токарно-винторезного станка от ходового винта и ходового вала. Данная задача может быть решена с помощью механических, гидравлических и электрических устройств.
Для ограничения хода выбирают схему и конструкцию в зависимости от назначения узла станка и требуемой точности. Ограничители хода предназначены:
для прекращения движения узла станка при достижении им предельного положения во избежание схода с направляющих или столкновения с другими узлами — предельные ограничители;
для выключения движения узла в строго определенной точке — размерные ограничители.
В качестве предельных ограничителей чаще всего используют конечные выключатели. Их обычная точность 0,5… 1,0 мм. Если часть станка, движение которой должно автоматически прекращаться, не имеет отдельного двигателя, то ход ограничивают разрывом кинематической цепи, и тогда используется любое устройство размерного ограничения хода.
Размерные ограничители срабатывают от жестких упоров, закрепленных на неподвижных частях станка, путем рассоединения кулачковых, шариковых, фрикционных муфт, падающего червяка, срабатывания гидравлического клапана.
https://extxe.com/3277/osnovnye-uzly-i-mehanizmy-stankov-i-tehnologicheskogo-oborudovanija/
https://cyberpedia.su/12x8f4b.html
https://studfile.net/preview/5332569/page:70/
https://goldpromo.com/blog/avtomatizatsiya-proizvodstvennykh-protsessov/
http://www.automationlab.ru/index.php/ispy/187-1
https://studfile.net/preview/635181/page:41/
Надёжностьсистемавтоматизации:конспектлекций[Электронныйресурс].–Режимдоступа: http://gendocs.ru/v37929/лекции_автоматизация_технологических_процессов_и_ про-изводств
Проектирование систем автоматизации технологических процессов: Справочное пособие/А.С.Клюев, Б.В.Глазов, А.Х.Дубровский, А.А.Клюев: Энергоатомиздат, 2013.
Печатные издания
Акимова Н.А., Котеленец Н.Ф., Сентюрихин Н.И. Монтаж, техническая эксплуатация и ремонт электрического и электромеханического оборудования: учебник – М.: ОИЦ «Академия», 2013г.
Быков А.В., Гаврилов В.Н., Рыжкова Л.М., Фадеев В.Я., Чемпинский Л.А. Компьютерные чертежно-графические системы для разработки конструкторской и технологической документации в машиностроении: Учебное пособие для нач. проф. образования/Под общей редакцией Чемпинского Л.А. - М.: Издательский центр "Академия", 2012г.
Технология машиностроения. Основы проектирования на ЭВМ : учеб. пособие / О. В. Таратынов, В. В. Клепиков, Б. М. Базров. — М. : ФОРУМ, 2017. — 608 с.
КарташовГ.Б.,Дмитриев А.В.Основы работы на станкахсЧПУ.–М.:Дидактическиесистемы,2012.
Клюев А.С. Монтаж средств измерений и автоматизации: справочник – М: Энергоатомиздат, 2012г.
Шишмарёв В.Ю. Автоматика. Учебник для среднего профессионального образования. – М.:Издательский центр «Академия», 2016. -288 с.
Технология машиностроения. Высокоэнергетические и комбинированные методы обработки: Учебное пособие / Аверьянова И.О., Клепиков В.В. -М.:Форум, НИЦ ИНФРА-М, 2016. - 304 с.
Технология машиностроения: Учебник / Клепиков В.В., Бодров А.Н., - 2-е изд. - М.:Форум, ИНФРА-М Издательский Дом, 2016. - 864 с.
Курсовое проектирование деталей машин: Учебное пособие/Чернавский С. А., Боков К. Н., Чернин И. М., 3-е изд., перераб. и доп. - М.: НИЦ ИНФРА-М, 2016. - 414 с.
Автоматизация производственных процессов в машиностроении : учеб. пособие / Е.Э. Фельдштейн, М.А. Корниевич. — Минск : Новое знание ; М. : ИНФРА-М, 2017. — 264 с.